Blog
Hammer Drill vs. Impact Driver: Choosing the Right Tool for the Job
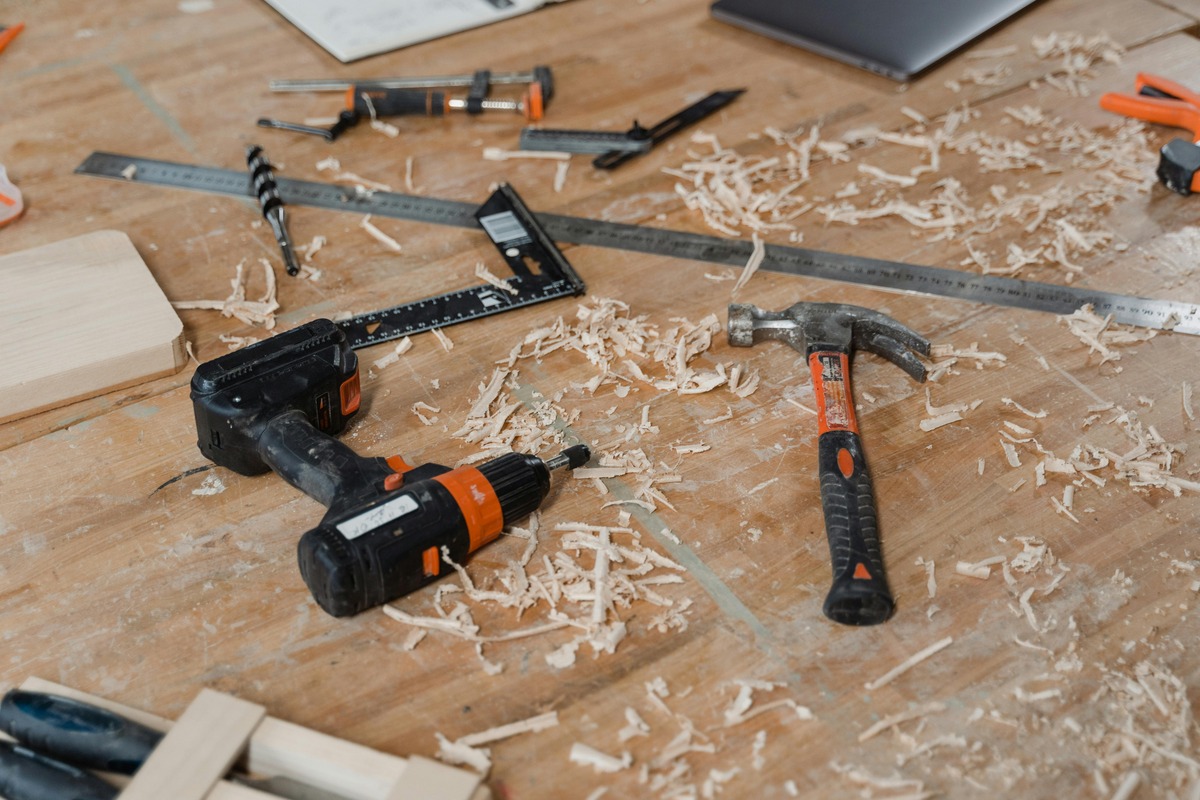
Power tools are indispensable companions in both DIY and professional toolkits, and among them, the hammer drill and the impact driver stand out as powerful workhorses designed for very different purposes. At a glance, they might appear similar—they're both handheld tools delivering high torque—but under the hood, they operate using distinct mechanisms tailored for specific tasks. Understanding their differences, strengths, and limitations is crucial to choosing the right tool for your next project.
Let’s dive deep into what sets the hammer drill and the impact driver apart.
Hammer Drill
A hammer drill is designed to bore holes into tough materials such as concrete, brick, and masonry. It combines rotational motion with a rapid hammering action along the same axis. Internally, two ribbed metal discs (called cams) rub against each other as the drill spins, creating a pulsating forward force. This action allows the drill bit to "punch" its way into hard surfaces while rotating—much like a chisel spinning in circles.
Key Features and Components
Chuck Type (Keyed or Keyless)
- Keyed Chucks: Require a special tool (chuck key) to tighten and secure the drill bit. These provide a firmer grip, especially when using larger or more heavy-duty bits.
- Keyless Chucks: Can be tightened by hand and are more common in modern models. They're quicker to change bits but may not hold as tightly under heavy stress.
- Bit Compatibility: Accept both round and hex-shanked bits, offering versatility for drilling in wood, metal, plastic, or masonry.
Hammering Mechanism
- Inside the hammer drill, two ridged discs (or cams) push against each other, causing the bit to move forward rapidly while rotating. This pulsating force helps the bit "chisel" into tough materials as it spins.
- The hammering function can usually be toggled on or off, allowing the drill to double as a standard rotary drill when the hammer function isn't needed.
Speed Settings (Variable Speed Control)
- Hammer drills often come with multiple speed settings (usually 2–3 gears) or variable speed triggers. Lower speeds are ideal for high-torque drilling, while higher speeds suit softer materials and quicker tasks.
- Some models also feature a clutch system that adjusts torque levels to prevent overdriving or damaging the bit or surface.
Impact Rate (BPM – Blows Per Minute)
- BPM measures how many hammer strikes the tool delivers per minute. A higher BPM means faster, more efficient penetration into hard materials.
- Typical ranges fall between 20,000 to 50,000 BPM depending on the model and power source (corded vs cordless).
Motor and Power Source
- Available in corded (more consistent power for heavy-duty work) and cordless (more portable and convenient) variants.
- Motors can be brushed or brushless, with brushless motors offering better efficiency, longer life, and less maintenance.
Primary Applications
Hammer drills shine when drilling into masonry, concrete, brick, and other dense materials where standard drills would fail or take too long.
Strengths of a Hammer Drill
- High torque output for tough drilling applications.
- Especially effective for larger diameter holes in concrete and stone.
- Versatile—can switch off the hammering function for regular drilling in wood or metal.
Limitations of a Hammer Drill
- Heavier and bulkier, making prolonged use more tiring.
- Less effective and often overkill for screw-driving or drilling into soft materials like wood or drywall.
- The hammering action can be too aggressive for precision work.

Impact Driver
Key Features and Components
Hexagonal Chuck (1/4-Inch Quick-Change)
- Uses a hexagonal collet that accepts only 1/4-inch hex-shanked bits.
- The quick-release mechanism allows for fast one-handed bit changes, improving speed and workflow on busy job sites.
- This system is designed specifically for driver bits, although drill bits with hex shanks are available.
- Uses a hexagonal collet that accepts only 1/4-inch hex-shanked bits.
Hammer and Anvil Mechanism
- The internal hammer and anvil system generates bursts of torque through rotational impacts rather than linear blows.
- As resistance increases (e.g., driving a screw into hardwood), the hammer slips past the anvil and slams into it rapidly, generating rotational force that would be difficult to match manually.
- This results in very high torque output with minimal kickback or strain on the user’s wrist.
- The internal hammer and anvil system generates bursts of torque through rotational impacts rather than linear blows.
Variable Speed Trigger
- Offers precise control over the rotational speed and torque output based on finger pressure.
- Crucial for preventing overdriving or damaging screws, especially in delicate materials or tight areas.
- Offers precise control over the rotational speed and torque output based on finger pressure.
Impacts Per Minute (IPM)
- IPM measures how many times per minute the hammer strikes the anvil to generate torque.
- Higher IPM values (often between 2,500 to 4,000) allow the tool to drive screws faster and with greater efficiency than standard drills.
- IPM measures how many times per minute the hammer strikes the anvil to generate torque.
Torque Output
- Impact drivers are designed for extremely high torque, often exceeding 1,500 inch-pounds, making them ideal for driving long or thick fasteners into dense materials.
- Some advanced models include torque adjustment settings or smart electronics to provide better control across a range of applications.
- Impact drivers are designed for extremely high torque, often exceeding 1,500 inch-pounds, making them ideal for driving long or thick fasteners into dense materials.
Compact Design and Ergonomics
- Typically smaller and lighter than hammer drills, making them ideal for overhead work or tight spaces.
- Many include rubberized grips, LED work lights, and belt hooks for convenience and user comfort during extended use.
- Typically smaller and lighter than hammer drills, making them ideal for overhead work or tight spaces.
Power Source and Motor Type
- Most impact drivers are cordless, relying on lithium-ion batteries (12V to 20V commonly).
- Brushless motors are increasingly common, offering longer runtime, more power, and better durability.
- Most impact drivers are cordless, relying on lithium-ion batteries (12V to 20V commonly).
Primary Applications
Primarily used for driving screws and bolts, especially in wood, metal framing, and automotive tasks.
Strengths of an Impact Driver
- High torque and rotational speed—perfect for driving long screws or lag bolts.
- Minimizes cam-out (slipping or stripping) of screw heads.
- Compact and lightweight, ideal for overhead work or tight spots.
Limitations of an Impact Driver
- Not designed for drilling into masonry or stone.
- May require impact-rated drill bits if used for light drilling tasks.
- Can be too powerful for delicate screws or soft materials, potentially damaging workpieces.
Key Differences Summarized
Feature | Hammer Drill | Impact Driver |
Mechanism of Action | Hammering + Rotation | Rotational Impacts |
Chuck Type | Keyed/Keyless | Hexagonal Quick-Change |
Primary Use | Drilling Hard Materials | Driving Screws and Bolts |
Noise Level | Loud (due to hammering) | Less loud, but high-pitched |
Control & Precision | Better for drilling | Better for driving fasteners |
How to choose wisely?
When to Choose a Hammer Drill
- When drilling into concrete, brick, or stone is required.
- For making larger diameter holes in tough materials.
- In scenarios demanding raw power and durability in masonry work.
When to Choose an Impact Driver
- Projects involving driving large volumes of screws or bolts.
- Tasks requiring speed, efficiency, and high torque.
- Working in tight spaces where a compact tool is essential.
- When you want to reduce wrist strain during repetitive fastening tasks.
Can You Use One Tool for Both?
While some overlap is possible, it's not ideal. An impact driver can perform light drilling with impact-rated drill bits, but it’s not suited for masonry or precise holes. Similarly, a hammer drill can drive screws, especially with a clutch setting, but it’s bulky, awkward, and lacks the finesse of a driver.
For those serious about DIY or construction, having both tools ensures you're covered—whether you're building a deck or installing shelves into brick walls.
Conclusion
The hammer drill and the impact driver each serve specific and essential roles in the tool world. Choosing between them isn't about which is better, but about what you're trying to accomplish. If you're frequently drilling into concrete or masonry, the hammer drill is your go-to. If you're assembling furniture, building a deck, or working with fasteners, the impact driver will make your job faster and easier.
For anyone regularly engaged in diverse tasks, investing in both tools offers the best of both worlds—powerful drilling and efficient fastening.